Wettstreit der Intralogistik-Ideen
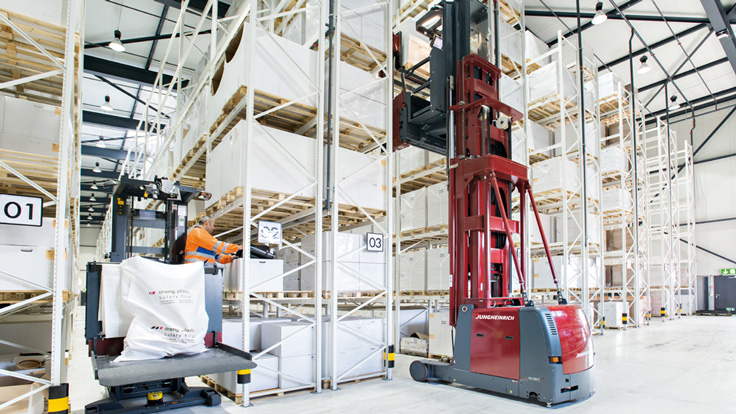
Keine andere Kategorie des Ifoy Awards stellt so hohe Ansprüche an die Jury wie die Bewertung der intralogistischen Lösungen. Hier geht es nicht nur darum, die Feinheiten komplexer Systeme und Ansätze hinsichtlich ihres Innovationsgrades zu bewerten, auch der Kundennutzen spielt eine große Rolle. Mit den beiden für den diesjährigen Ifoy Award eingereichten Bewerbungen standen zwei spannende Konzepte auf dem Prüfstand: Toyota Material Handling präsentierte den Praxiseinsatz des Flottenmanagementsystems I-Site beim spanischen Logistikdienstleister Carreras. Jungheinrich dagegen hatte sich mit einer kompletten Lagerlösung beworben.
Paket zur Kostensenkung
Bei der Implementierung des I-Site-Systems von Toyota MH ging es Carreras um klar definierte Ziele: Zum einen sollte der Warenumschlag optimiert werden, zum anderen sollte die Schadenquote der Flurförderzeuge deutlich geringer werden, und schließlich sollten auch die Betriebskosten der Flurförderzeugflotte sinken. Die im vergangenen Jahr eingeführte Lösung unterstützt die Anwender bei Carreras dabei, den Einsatz der gesamten Flotte mit Hilfe des benutzerfreundlichen und leicht zugänglichen Webportals besser zu überblicken. Doch beschränkt sich der I-Site-Ansatz nicht nur darauf, die technischen Möglichkeiten für eine Optimierung der Betriebsabläufe zu gewährlkeisten. Zweites Standbein ist die permanente, begleitende Beratung durch den Anbieter.
Diese Kombination trug bei Carreras rasch Früchte: Allein im Jahr 2011 stieg die Produktivität in den Logistikzentren, bei denen I-Site eingesetzt wurde, um 10 Prozent, während die Betriebskosten der Staplerflotte um rund 60 Prozent sanken. Basis für Letzteres war die Kontrolle und Optimierung der Arbeitsabläufe: Hierbei wurden die Fahrzeiten gemessen und neue Aufnahmepunkte für die Paletten definiert.
Das Monitoring brachte einen zweiten positiven Effekt mit sich: Da sich jeder Staplerfahrer über einen individuellen Pin-Code an seinem Fahrzeug anmelden muss, ist einerseits gewährleistet, dass nur geschultes, autorisiertes Personal die Geräte in Betrieb nehmen kann. Auf der anderen Seite lässt sich so jederzeit nachvollziehen, welcher Fahrer das Gerät zu welchem Zeitpunkt bedient hat. Diese Transparenz führte dazu, dass die Zahl der Kollisionen und Unfälle spürbar zurückging, da über I-Site die Verursacher einwandfrei ermittelt werden konnten. Um die Fahrer mit ins Boot zu holen, führte Carreras parallel ein Anreizsystem für die Vermeidung von Schäden ein.
Aus einer Hand
Die Streng Plastic AG, ein Schweizer Hersteller von Kunststoffrohrleitungssystemen, musste dringend ihre Lagerkapazitäten ausbauen. Nach einer ersten Planungsphase wurde Jungheinrich als Generalunternehmer ausgewählt, auf einer sehr begrenzten Grundfläche ein Hochregallager mit über 4000 Palettenstellplätzen zu errichten. Nach einer Anforderungs- und Materialflussanalyse fiel die Wahl auf ein Schmalganglager mit Lagernavigation. Der Flurförderzeughersteller lieferte dabei das gesamte Regalsystem, die Flurförderzeuge, das Lagerverwaltungssystem Jungheinrich WMS und die notwendige Datenfunkstruktur.
Kernelement des Projekts war hierbei nicht die Hard-, sondern die Software. Auf der einen Seite implementierte Jungheinrich das eigene Warehouse Management System. Dieses unterstützt nicht nur alle Materialflussprozesse unter Berücksichtigung des Lagerlayouts, der Fahrzeuge und der Waren, es kommuniziert dazu mit dem ERP-System von Streng Plastic.
Im Fall des neuen Lagers kam eine Besonderheit hinzu: Die Arbeitsabläufe der Schmalganggeräte sollten mithilfe der Jungheinrich-Lagernavigation optimiert werden. Hierzu mussten die Geräte über das Middleware-Paket "Logistik-Interface" an das WMS angebunden werden. Die Schnittstellensoftware übermittelt nun alle Fahraufträge direkt aus dem WMS an die Fahrzeugsteuerung. Der Staplerfahrer muss nur noch Gas geben. Die erreichte Zielposition wird zudem in Echtzeit an das Jungheinrich WMS bestätigt. Damit die Daten jederzeit uneingeschränkt zur Verfügung stehen, installierte der Generalunternehmer auch die passenden Datenfunkkomponenten und -dienstleistungen.
Dank der neuen Intralogistiklösung läuft der Materialfluss im Lager des Kunststoffröhrenherstellers deutlich zuverlässiger und effizienter als zuvor: Die Lagernavigation reduzierte die Fehlerquote bei Ein- und Auslagerungen auf 0 Prozent. Gleichzeitig stieg die Effizienz des Schmalganglagers um bis zu 25 Prozent. Die Investition amortisierte sich nach Aussagen des Streng-Plastic-Managements - bei Schweizer Betriebs- und Personalkosten - bereits nach wenigen Monaten. Zudem bietet das Lager noch Ausbaureserven, da die einzelnen Elemente modular erweiterbar sind.