Kleben statt stretchen
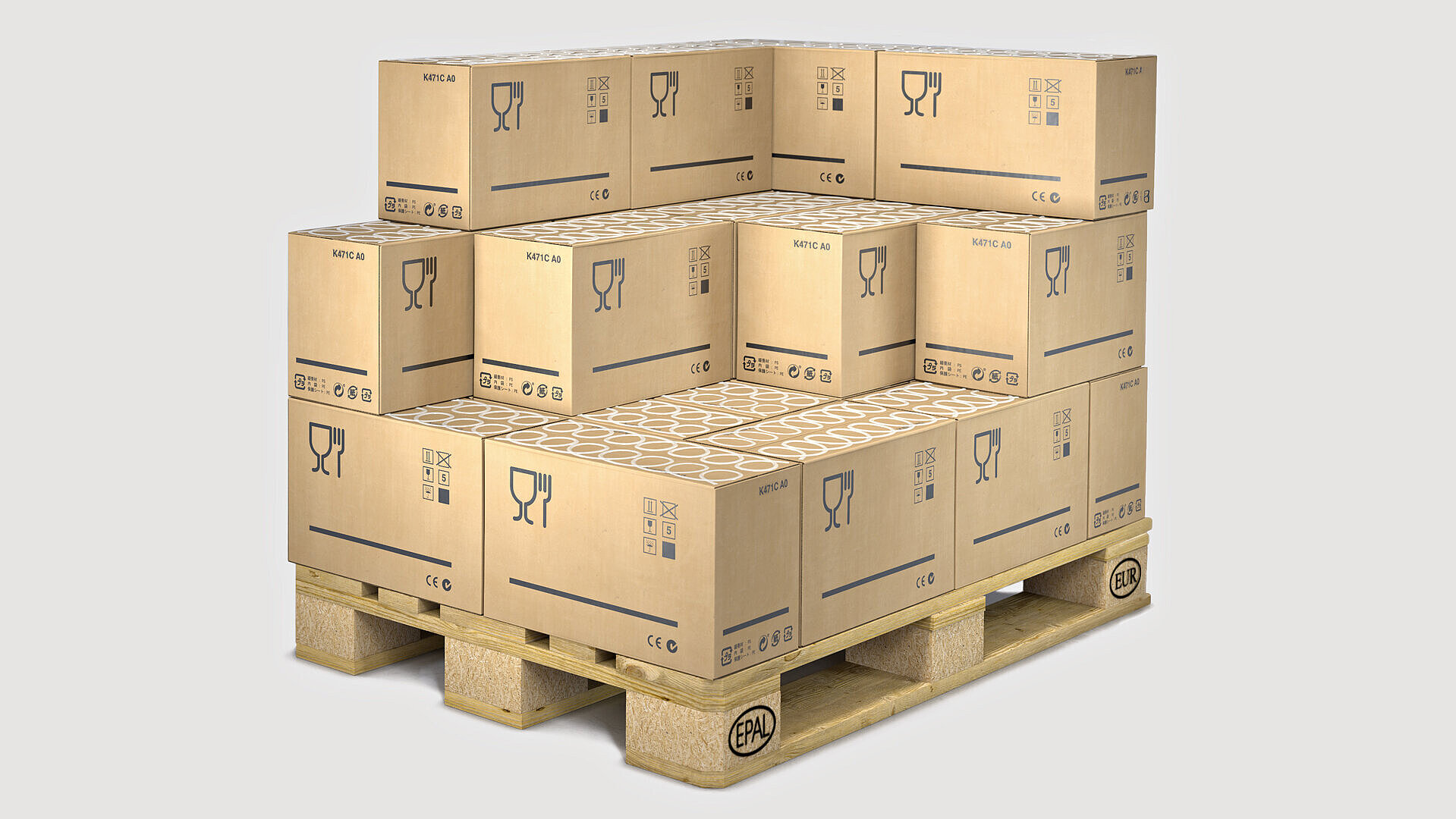
Die Geschäftsidee eignet sich bestens für einen Elevator-Pitch: Könnte man nicht auf das Umwickeln der Kartons und Säcke mit Kunststofffolie beim Palettieren verzichten? Wie wäre es, wenn das Sichern von Packstücken auf der Palette auch mit einem Klebstoff möglich wäre? Schließlich kostet der Einsatz der Folie nicht nur Geld, sondern braucht Energie, verursacht Emissionen und Abfall. Genau so eine Lösung hat der Düsseldorfer Konsumgüter- und Kelbstoffkonzern Henkel in den vergangenen Jahren entwickelt.
„Bisher wird beim Palettieren, beispielsweise von Paketen, zuerst eine Antirutschmatte auf die Palette gelegt. Darauf folgt eine Lage Kartons und eine Zwischenlage, die meist aus Pappe besteht, dann die nächste Schicht Kartons und wieder eine Zwischenlage und so weiter, bis die Palette schließlich mehrfach mit Kunststofffolie umwickelt wird“, erläutert Henkel-Marketingmanager Daniela Tonn. Anders verhält es sich mit den Heißklebestoffen: „Vor der Palettierung wird der Klebstoff auf die Verpackung aufgetragen, wobei geringe Mengen ausreichen“, fügt Marktstrategie-Managerin Felicia Forster hinzu.
Klebstoffmenge variiert
Wieviel Klebstoff benötigt wird, hängt von mehreren Faktoren ab. Was man den Henkel-Managern zufolge sagen kann: Der Klebstoff wird nicht flächig, sondern hauchfein aufgetragen, beispielsweise spiralförmig, in Linien oder Raupen. Tonn: „Das hängt davon ab, was palettiert wird – ob Säcke oder Kartons, wie groß die Verpackungsfläche ist, aus welchem Material die Verpackung besteht, also ob etwa der Karton lackiert ist, und wie hoch der Anteil an recycelten Papierfasern ist.“
Zum Hintergrund: Wenn der Recyclinganteil hoch ist, sind die Papierfasern sehr kurz, wenn es Frischfaser ist, sind die Fasern sehr lang. Und das wirkt sich entsprechend auf die Wahl des Klebstoffs aus, da sich die Haftung unterscheidet. Es geht aber auch darum, wie schwer und beweglich das Füllgut ist – und wie schwierig es ist, die Gesamtstabilität der Palette zu gewährleisten. Außerdem kommt es auch darauf an, ob die Palette bei der Lagerung und beim Transport etwa großer Hitze oder Kälte ausgesetzt ist.
All diese Faktoren muss man kennen, um zu wissen, welcher von etwa fünf verschiedenen Klebstoffen in welcher Menge verwendet wird und welcher Auftrag der richtige ist. „Das wird von unseren Kolleginnen und Kollegen im Vertrieb und im technischen Kundendienst immer individuell für jeden Kunden betrachtet und bewertet“, sagt Tonn.
Raue Oberfläche
Bevor der Schmelzklebstoff aufgetragen werden kann, muss er erhitzt werden – ähnlich wie im Hausgebrauch bei einer Heißklebepistole. In der Regel sind das 180 Grad Celsius. Nach dem Auftragen ist er jedoch nicht so klebrig, dass er etwa am Finger haften bleibt. Wenn man zum Beispiel mit dem Finger über den spiralförmig aufgetragenen Klebstoff streicht, fühlt sich das eher wie eine sehr raue Oberfläche an. „Vereinfacht ausgedrückt, kommt es nicht auf die Klebrigkeit an, sondern auf die rutschhemmende Wirkung des Klebstoffauftrags“, sagt Tonn.
„Zum Teil wird auch hier eine Antirutschmatte eingesetzt“, ergänzt Forster. Diese könne aber auch weggelassen werden, je nach Anforderungen an die Palette. Der Vorteil: „Man braucht – anders als beim herkömmlichen Prozess – keine weiteren Zwischenlagen mehr. Und es entfällt das Umwickeln mit der Folie zur Stabilisierung. In geringerer Menge wird diese aber noch als Staub- oder Sichtschutz verwendet.“
Bis zu 90 Prozent Verpackungsmaterial lassen sich laut Forster durch die Lösung bei Folie und Zwischenlagen einsparen – „und damit dann auch bis zu 90 Prozent an Materialkosten“. „Umgerechnet sind das in einem repräsentativen Beispiel bis zu 87 Prozent CO₂-Einsparung im Vergleich zum herkömmlichen Palettisierprozess.“ Die genaue Reduktion richtet sich danach, um welche Zwischenlagen und Folien es sich handelt. Im Anwendungsfall eines Kunden konnten die Kosten für eine Palette nach Henkel-Angaben durch die erhebliche Materialeinsparung von 4,55 auf 2,15 Euro gesenkt werden.
Ein weiteres Plus: „Auch wenn man den Klebstoff auf Kartonage, Papier- oder Plastiksäcke aufträgt – er ist kompatibel mit dem Recyclingprozess“, sagt Tonn. „Und wir achten bei den Formulierungen darauf, dass wir nachhaltige Rohstoffe verwenden und sich der Prozess drumherum effizienter gestalten lässt“, fügt Forster hinzu. Dies sei zertifiziert durch das unabhängige Institut Cyclos-HTP, das sich darauf spezialisiert hat, Recyclingkompatibilität von Verpackungen zu bemessen. Zudem ist eine Wiederverwendung möglich: „Je nach Verpackung, kann auch mehrfach palettiert werden.“
Auch das Depalettieren werde vereinfacht. „Die Zwischenlagen werden nicht mehr benötigt und weniger Kunststofffolie muss entfernt werden“, sagt Forster. Das wirke sich positiv auf den Prozess insgesamt aus, was in Zeiten des Fachkräftemangels ein wichtiger Aspekt für die Industriekunden sein könne. Auch ein automatisiertes Depalettieren sei aufgrund der fehlenden Zwischenlage möglich, da diese immer manuell entfernt werden müsse. Je nach Füllgut sei es zudem möglich, höher zu stapeln.
Bisherige Anwender will der Konzern nicht nennen, die Lösung werde aber zum Beispiel auch im eigenen Haus von der Konsumgütersparte genutzt. Die Nachfrage steige, heißt es lediglich. Das liegt möglicherweise auch an der neuen EU-Verpackungsverordnung Packaging & Packaging Waste Regulation (PPWR), über die im Herbst im Rat der Europäischen Union final abgestimmt werden soll. Diese sieht eine Verschärfung der Anforderungen an die Recyclingfähigkeit von Verpackungen und den Einsatz von Rezyklaten vor – und fordert unter anderem die hundertprozentige Wiederverwendung bestimmter Industrie- und Gewerbeverpackungen. (fw)