VW-Logistiker: „Batterieproduktion ist eine ganz andere Welt“
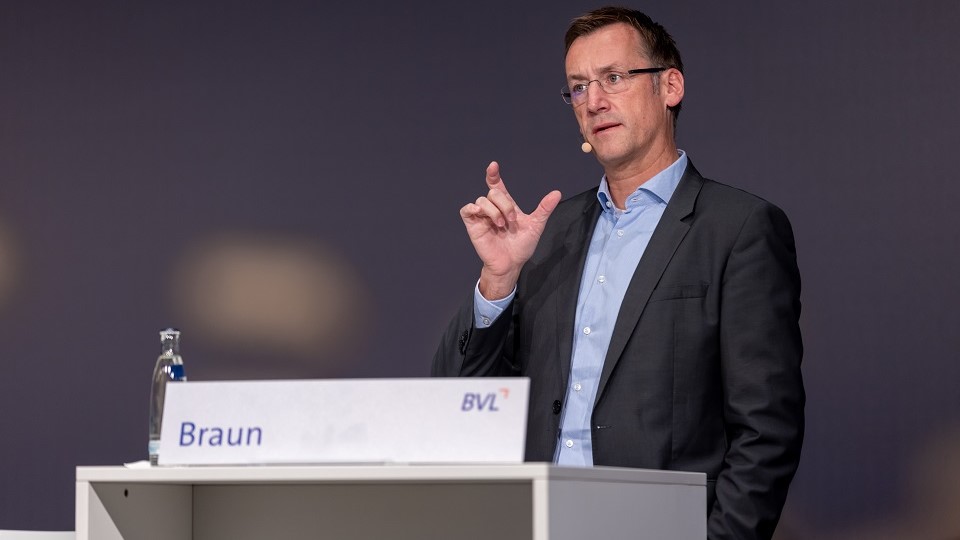
Die Autoindustrie steht vor einem großen Wandel und muss ihre Produktionsabläufe angesichts des Trends zur E-Mobilität verändern. Auch der Autobauer Volkswagen plant, in den kommenden Jahren den Anteil von E-Autos deutlich zu erhöhen. Der Wertschöpfungsanteil des E-Antriebs sei signifikant groß, sagt Matthias Braun, Leiter Logistik der Volkswagen-Tochter Powerco. Er sprach am Donnerstag beim Deutschen Logistik-Kongress in Berlin.
Mit dieser Erkenntnis steigt der Konzern selbst in die Produktion der E-Antriebe ein. Ein weiterer Grund ist, dass der Markt für die Batteriezellen in der Hand weniger großer Firmen in Asien liegt. In solch eine gefährliche Abhängigkeit will sich Volkswagen nicht begeben. Da der Markt auch insgesamt wachse, gehe es auch darum, die Versorgungssicherheit nachhaltig abzusichern, fügt Braun hinzu. Deswegen hat der Autobauer im Juli das Unternehmen Powerco gegründet. In dieser Firma mit Sitz in Salzgitter fasst der Konzern die gesamten Aktivitäten für die Batterie-Wertschöpfungskette zusammen.
Sechs europäische Fabriken
In Salzgitter wird der Konzern auch die erste Batteriezellfertigung starten. Als weiterer Standort für eine Gigafactory steht bereits Valencia (Spanien) fest. Weitere Fabriken würden laut Braun „sehr wahrscheinlich eher im Osten Europas gebaut“, aber auch in Nordamerika werde eine entstehen. Volkswagen will mit Partnern gemeinsam bis Ende des Jahrzehnts in sechs europäischen Fabriken Elektroauto-Akkus mit einer Leistung von 240 Gigawattstunden jährlich herstellen.
Dieses neue Produktionsnetz erfordert eine ausgeklügelte Logistik. „Mit dem Bau von Batteriezellen tauchen wir in eine ganz andere Welt ein“, sagt Braun. So sei zum Beispiel die Lieferantenbasis eine komplett andere als im bisherigen Automobilbau. Eine Herausforderung sei auch das Thema Verpackung für die Materialien. In den Prozessen bestehen extrem hohe Anforderungen an die Sauberkeit. Das gelte auch für die Produktion selbst. „Schon ein Raucher ohne Mundschutz wäre eine Gefahr“, sagt Braun. Partikel könnten die Qualität einer Batteriezelle beeinträchtigen. Diese Anforderungen führen laut Braun innerbetrieblich „zu vielfach gebrochenen Prozessen“.
End-to-End-Kette aufbauen
Für den Transport der fertigen Batteriezellen setzt Volkswagen auf die Bahn. Bei den Prozessen werde Built-to-Order auf Built-to-Stock treffen, ergänzt Braun. „Denn wir werden auf Lager und unsere Fahrzeugwerke nach Kundenauftrag produzieren.“ Bei den Prozessen, die der Batteriefertigung vorgelagert sind, müsse Volkswagen zudem ganz andere Wege gehen, um sich die Rohstoffe zu sichern.
Hier gehe es weit über die Stufe der 1st-Tier-Lieferanten hinaus. Braun spricht von einer „kompletten horizontalen Integration unserer Partner innerhalb der Prozesskette“. Und das alles – die gesamte Kette von einer Mine bis zum Verbau der Zelle im Fahrzeug – gelte es aktiv zu steuern, zu beeinflussen, mitzugestalten und zu kontrollieren. Hinzu komme dann natürlich noch der Recyclingprozess. „Daraus ergibt sich eine einmalige Chance, jetzt innerhalb der Automobilindustrie eine End-to-End-Kette aufzubauen.“ Funktionieren könnte dies alles in etwa zwei bis drei Jahren, schätzt Braun.
Batteriematerialienfirma gegründet
Die Batteriesparte des Volkswagen-Konzerns und der belgische Materialtechnologiekonzern Umicore haben kürzlich erst ein milliardenschweres Gemeinschaftsunternehmen für Batteriematerialien gegründet. Das Joint Venture von Powerco und Umicore mit Sitz in Brüssel will 3 Milliarden Euro investieren und Ende des Jahrzehnts Materialien für 2,2 Millionen Elektroautos jährlich liefern, wie die Unternehmen im September mitteilten.
Mit den Batteriekomponenten wollen die Firmen einen großen Teil des Bedarfs der geplanten europäischen Batteriezellfabriken decken. Vorwiegend geht es dabei um Batterie-Kathoden und Vormaterialien für 160 Gigawattstunden an Zellkapazität. (mit dpa)